從“優生優育”談質量預防
聯系電話
聯系電話
關注我們
公眾號
關注公眾號 獲取更多靈感
- 返回頂部
質量預防,應從哪里入手?
發布時間:
2024-05-07 00:12
我曾經在《質與量的戰爭》中介紹了格魯庫克博士質量鏈的“三分法”,即把一個完整的企業核心業務鏈條劃分成三個階段,分別是:
1、從市場/銷售到設計/開發,主要負責產品質量;
2、從采購、制造到交付,主要負責交付質量;
3、從物流到服務,主要負責支撐質量。
這個產品從無到有的價值實現的“生產”過程,和我們熟悉的母親“生產”過程何其相似!
女性生孩子的過程,原本就分為三個階段:第一個階段是十月懷胎,第二個階段是進產房,第三個則是坐月子。
當我們在談及優生優育的話題時,意圖明確,就是為了生一個健康聰明的寶寶。于是,每個人都會不自覺地遵循著一個常識性的自然法則,那就是我們所謂的“優生法則”——“十月懷胎”更加關鍵。
從中,我們可以解讀出三個簡單而關鍵的問題。
其一,我們一直以來都把工廠當作一個活的生命體來看待,看企業也是這樣,也是活的;反之,西方人總是傾向于把企業看作是一個沒有生命的賺錢機器,是死的。所以,我們有“百年老店”的概念一一活的東西才有可能存在百年、千年,他們只有成功與失敗的概念,如今升級為永續經營、可持續發展的概念。
其二,優生優育需要預防,而重視“十月懷胎及以前”,就是預防。這與我們常規的思路是相逆的。因為人們常常關注看得見的東西,而忽略看不見的東西。顯然,看不見的才更加關鍵。
其三,我們在談品質與預防,就像是在談優生優育。然而在現實中,那些所謂抓“生產”品質的人們則完全違背了優生優育的自然法則。比如,在許多公司,質量人員占總人數的5%~8%,甚至更多。問題是他們都在哪里呢?答案是,絕大多數人都在“產房”——生產車間里面忙著呢。
舉個例子。
某家企業,全部的質量人員有近400人;
在“十月懷胎”的地方,市場和銷售沒有人,研發系統大概有200多人;
在“坐月子”的地方,亦即后端的服務過程,大概有四五個人。
那么,大多數人在哪里呢?都在“產房”。
如果我們再能夠聯想到核心業務流程“端到端”的集成與數據鏈條的打通問題,再一次在腦海中匹配“影響成本的模型”圖,那么就更要嘗試一下我給大家的建議了:回家去,向家里的那位“廠長”請教,然后把“優生法則”更好地運用到企業里面。
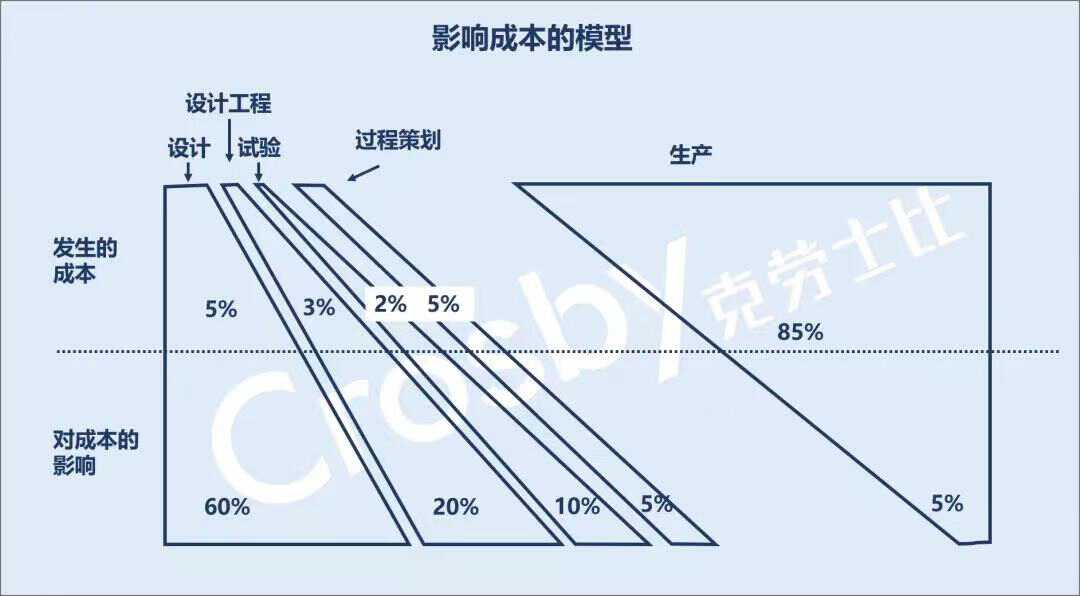
這里的所謂“匹配”是有切實的含義和真切的情景的。雖然它是通過財務的角度對成本產生影響,做了量化的表達和對比,但它似乎說的就是我們現實中質量管理資源的分配現狀與問題產生的原因一一原來我們是循著看得見的或成本產生的因素去分配資源的。
比如實際發生的成本:設計占5%,設計工程3%,試驗2%,過程策劃5%,而生產則高達85%。也許正是由于它們是實實在在發生的、看得見的,才牽引著管理的資源尤其是質量管理的資源進行了“橄欖球型”的配置。
而對成本的真正影響,則正好反了過來:生產環節僅僅占5%,而設計、工程和試驗方面,加在一起高達90%。當然,這還沒有包含銷售、戰略與營銷,不過可以想象,它們對成本的影響更是大得驚人。
這就再一次印證了我們“治理長江要從源頭抓起”,尤其是零缺陷之“零進零出”原則的正確性和實效性。
正如克勞士比學院反復強調的那樣,成本和PONC讓人們突然對品質有了意識,對預防有了意識。因為所謂意識,就是人們對某些事情關注的程度與水平。這也就是我們要用價值和金錢來衡量質量的原因。
只有當預防和成本碰撞在一起的時候,才能激起預防的火花,也才有可能產生實際的行動,以及想要達成的結果。
華為公司的銷服系統很早就開始抓質量了。
十幾年前,當時的負責人胡厚崑在明白了“治理長江”的意義之后,便要求每一個國家部和地區部總裁都要成為首席質量官,并使用了公司特有的考核的方式,將質量的管理責任“回歸”到他們身上——也就是我反復強調的“司機歸位”的主張。
其意圖非常明確,那就是要緊緊地抓住“合同質量”這個牛鼻子,將合同作為所有工作的中心,以推動整個系統工作流程的改進。當然,關鍵就是在流程的改進過程中,將質量的要求和標準不斷優化,然后構筑進去。
后來,他們又有了要在銷服系統設立QA人員的需求,再后來,就開始設立質量組織了。因為他們已經在實踐中認識到,把流程打造好,配上QA進入執行流程的團隊,就會提升能力;把LTC(線索到現金)流程執行好,自然而然就能夠保證輸出高質量的合同。而QA的核心作用,就是要保證輸入輸出各環節的高質量。
同時,建立“質量回溯”與問責機制,以促使大家去不懈地追求高質量;還要落實公司的“質量審計”要求,不僅審查LTC是不是全流程關注了質量,而且重要的是審計流程執行過程中是否有問題。最后,在國家部和地區部層面設立首席質量官。
GT公司,由于客戶端出現了批量事故,造成訂單的減少和經營的困難。于是,便開啟了“管理變革年”,變革的主題有很多,但最易行的只有兩個:提升品質和降低成本。
質量系統在進行質量戰略解碼的過程中,達成了“成就客戶價值,助力經營績效”的共識。然后,將企業的經營指標逐一解碼成質量的控制指標或質量經營的價值貢獻指標,包含了三個方面,質量團隊的優化,PONC減少以及市場不良率的減少。
為此,一方面對質量團隊的人才結構以及人員構成和分布進行排查診斷,以提出改進的方向與有效舉措。
分析表明:在全集團超1000人的龐大的質量隊伍中,超過38%的是制造過程的QC,主要在做問題攔截的工作;而在客戶端只有4%的人員,設計系統的QA也只有8%,物料部分占了11%,產品可靠性測試占了9%,出貨占了3%,供應商質量管理占了4%。
于是,他們提出“產房里面鬧革命”的方案,加大源頭的資源布控,培養更多的BP(業務伙伴)和質量專家,將生產現場的QC減少10%,以共同完成在客戶端的“雙零”目標,即零投訴和零退貨。
一年后,效果顯著。不僅連續榮獲其關鍵客戶頒發的金牌供應商榮譽,追加了訂單,而且實現了P0NC削減30%的目標,整個團隊得到了公司重獎。
TM公司,在頓悟了“優生優育”的道理之后,便開始對現有的質量隊伍尤其是專家人員進行盤點。
然后,將更多的資源向前端的市場、研發以及后端的供應商管理分配,相應地增加了客戶關系改善工程師、研發質量工程師、流程工程師以及供應商質量管理工程師;而對于制造端,則強調質量工程師、工藝工程師與制造工程師的協同作戰。
他們基于“符合要求鏈”來優化整個的流程,設定了全鏈條質量要求的關鍵閘口,由質量部門的人員進行管控,而原來那些過程中的檢驗檢查人員,便融入了生產管理流程之中。
這樣一來,不僅定位清晰了,目標明確了,人員精簡了,而且對于公司構建端到端的業務流程的變革項目,起到了積極的建設性的作用。當然,其效果也是顯而易見的。
上一頁
上一頁
更多資訊
2024-06-30
2024-05-07
2024-04-10
2024-03-28
2024-03-12